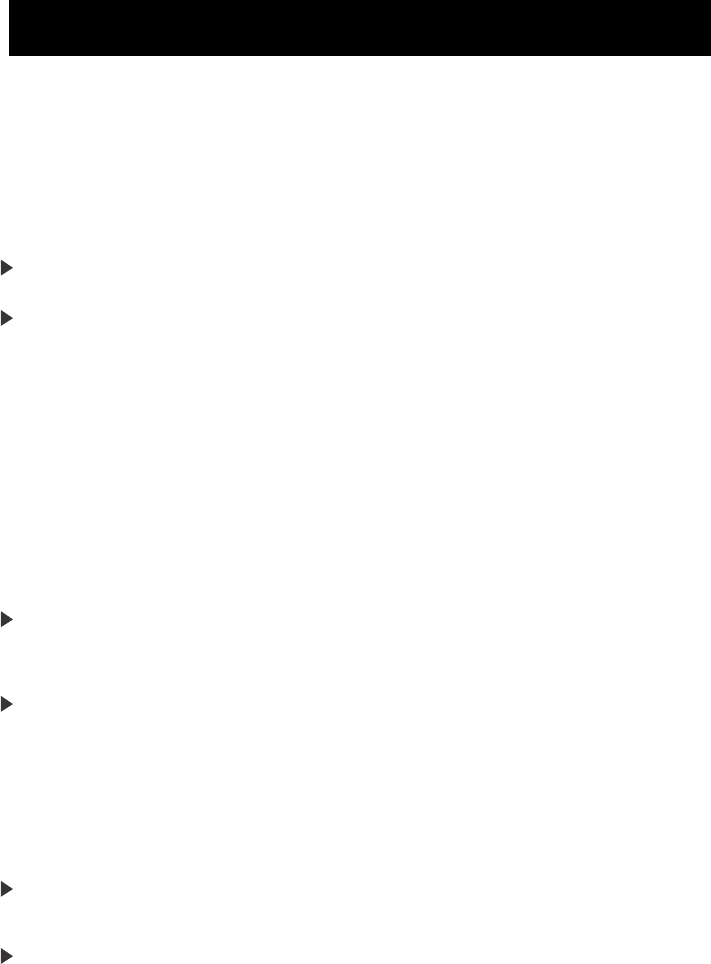
DANGER To reduce the risk of injury, do not permit children to use this product unless they are
closely supervised at all times.
WARNING - RISK OF CHILD DROWNING. Extreme caution must be exercised to prevent
unauthorized access by children. To avoid accidents, ensure that children cannot use a spa
or hot tub unless they are supervised at all times.
DANGER To reduce the risk of injury to persons, do not remove suction fittings.
Spa location must accommodate sufficient drainage of water around the base of the structure, as
well as the power source compartment.
Prolonged immersion in water that is warmer than normal body temperature can result in a
dangerous condition known as HYPERTHERMIA. The causes, symptoms, and effects of
hyperthermia may be described as follows: Hyperthermia occurs when the internal
temperature of the body reaches a level several degrees above the normal body
temperature of 98.6F. The symptoms of hyperthermia include dizziness, fainting,
drowsiness, lethargy, and an increase in the internal temperature of the body. The effects of
hyperthermia include (1) unawareness of impending hazard, (2) failure to perceive heat, (3)
failure to recognize the need to exit spa, (4) physical inability to exit spa, (5) fetal damage in
pregnant women, (6) unconsciousness resulting in danger of drowning. WARNING The
use of alcohol, drugs or medication can greatly increase the risk of fatal hyperthermia in hot
tubs and spas.
DANGER - RISK OF ELECTRICAL SHOCK. Install at least 5 feet (1.5m) from all metal surfaces.
(A spa may be installed within 5 feet of metal surfaces if each metal surface is permanently
connected by a solid copper conductor attached to the wire connector on the terminal box
that is provided for this purpose. Refer to NEC and local codes in effect at the time of
installation.)
A pressure wire connector is provided on the control box to permit connection of a solid copper
bonding conductor between this point and any equipment, metal enclosures of electrical
equipment, metal water pipe, or conduit within 5 feet (1.5m) of the unit as needed to comply
with local requirements.
Bond accessible metal to the dedicated connector on the equipment grounding bus, bond the
equipment ground bus to the local common bonding grid as part of the installation in the
form of (1) a reinforced concrete slab for support, (2) a ground plate provided beneath the
hot tub or spa, or (3) a permanent ground connection that is acceptable to the local
inspection authority.
DANGER RISK OF ELECTRICAL SHOCK. Do not permit any electrical appliance, such as a
light, telephone, radio, or television, within 5 feet (1.5m) of a spa or hot tub.
To reduce the risk of injury:
The water in a spa or hot tub should never exceed 104F (40C). Water temperatures between
100F (38C) and 104F (40C) are considered safe for a healthy adult. Lower water
temperatures are recommended for extended use (exceeding 10-15 minutes) and for young
children.
Excessive water temperatures have a high potential for causing fetal damage during the early
months of pregnancy, pregnant or possibly pregnant women should limit spa or hot tub
water temperatures to 100F(38C).
IMPORTANT SAFETY INSTRUCTIONS
READ AND FOLLOW ALL INSTRUCTIONS
!
!
!
!
!
2